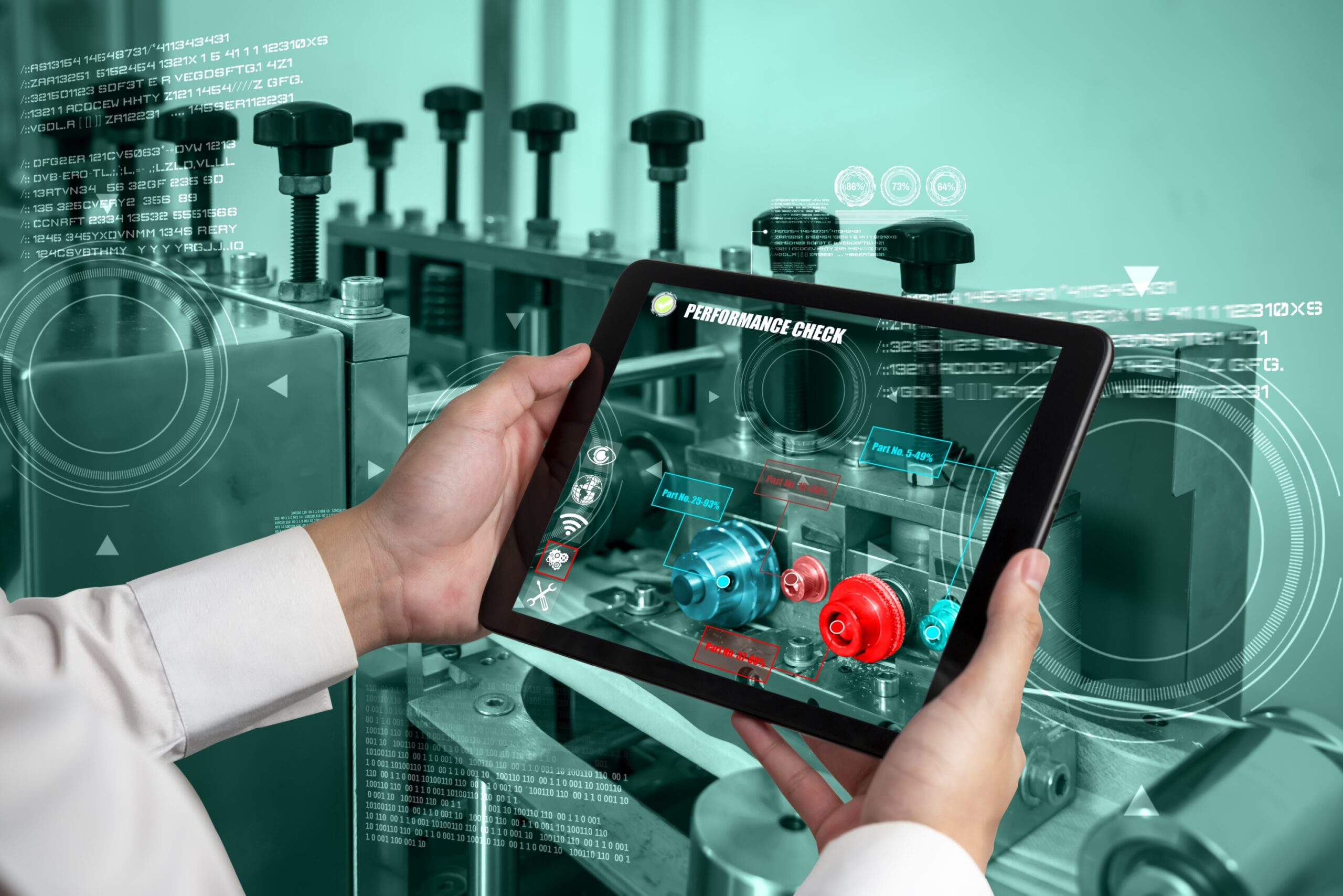
Safety Management System Implementation
Industries often viewed accidents as inevitable and acceptable. However, a multinational corporation (MNC) faced significant challenges in improving its safety
This paper presents a case study conducted in a chemical plant with a cogeneration facility, focusing on optimizing boiler shutdown timing to enhance availability and reliability and minimize downtime during annual inspections. The study addresses two key problems faced by the plant, namely scaling in the furnace and prolonged annual shutdown periods required for repairs, replacements, cleaning, and inspections. The assigned BiC promoter from a consulting firm took charge of implementing improvements and demonstrated effective leadership throughout the process. This paper outlines the approach adopted for each problem, the action points undertaken, and the corresponding results achieved.
The chemical plant heavily relies on pulverized coal-fired boilers, with two larger boilers accounting for 80% of the energy supply. The issues of scaling in the furnace and extended annual shutdowns have significant implications for the plant's production, profitability, and compliance with Indian boiler regulations.
Problem 1: Scaling in the furnace and low-temperature zone leads to frequent shutdowns for cleaning, resulting in production loss and decreased profitability.
Problem 2: Lengthy annual IBR boiler shutdowns of 21 days impact revenue and customer satisfaction.
Problem 1 Approach: Historical data analysis was conducted to identify the cause of scaling. It was discovered that the fuel had been changed from bituminous coal to sub-bituminous coal. The fusion temperature of the sub-bituminous coal caused ash to melt and solidify, leading to scaling. The assigned promoter, from a consulting firm, proposed a solution involving the procurement of coal from an Indonesian mine with a higher fusion temperature.
Problem 2 Approach: A collaborative approach involving the assigned BiC promoter, plant engineers, experienced workers, and contract workers were undertaken to address the extended shutdown period. The critical path analysis revealed opportunities for parallel activities and series activities. Emphasis was placed on converting series activities to parallel ones, ensuring preparedness with spare parts, and employing modern tools and experienced teams.
Problem 1 Solution: The assigned BiC promoter visited an Indonesian coal mine, discussed the technical requirements, and established an agreement to procure coal with the desired fusion temperature. A standard operating process was established to ensure uninterrupted boiler operation and reduce costs.
Problem 2 Solution: The assigned BiC promoter led the optimization efforts by maximizing parallel activities, ensuring the availability of spare parts, and increasing the number of contract workers. The workforce was incentivized to improve efficiency, and accountability was assigned to all stakeholders. As a result, the annual shutdown duration was reduced to five and a half days, meeting quality standards and regulatory requirements.
The success of this case study can be attributed to the effective leadership and dedication of the assigned promoter. BiC consulting farm has expertise in all kinds of technology on coal gas oil and petroleum coke used to resolve such critical challenges as well as the selection process of coal suitable for the Boilers.
Industries often viewed accidents as inevitable and acceptable. However, a multinational corporation (MNC) faced significant challenges in improving its safety